Technological advancements and improving processes in the mining industry ultimately aim to improve safety, productivity and sustainability. Over the last 40 years, one such area of development has been sprayed concrete as a part of the support system for underground mines and tunnels
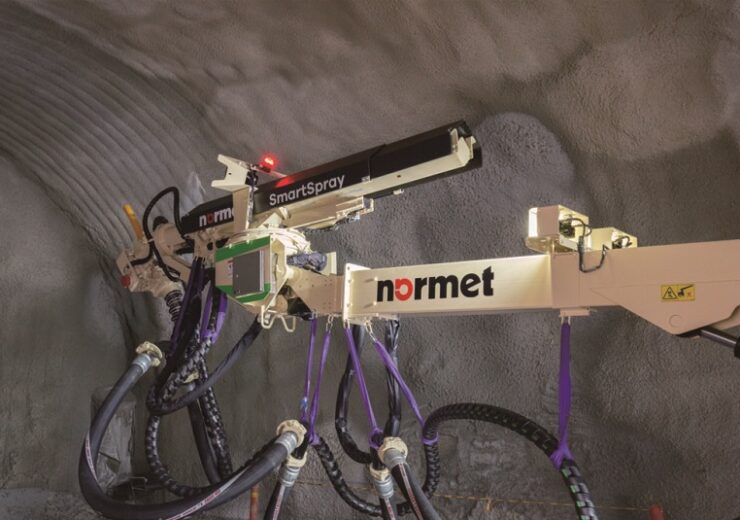
Normet has designed intelligent software that works with spraying robots. (Credit: Normet)
Technological advancements and improving processes in the mining industry ultimately aim to improve safety, productivity and sustainability. Over the last 40 years, one such area of development has been sprayed concrete as a part of the support system for underground mines and tunnels.
Concrete spraying is a time and cost-effective, mechanised technological solution for shaft lining and concrete construction. Application methods for sprayed concrete only continue to improve, especially when utilising digitalisation to ensure optimised layer thickness and reduce CO2 emissions. The automatisation of sprayed concrete not only improves efficiency but also simplifies the process for the operator, requiring fewer worker resources.
As with any step towards digitalisation, the collection of data and the ability to effectively analyse this information has revolutionised the way that informed decisions can be made during tunnelling projects. This reflects an industry-wide trend towards the Building Information Modelling (BIM) and 3D model-based processes during planning, designing and construction. Analysing and exchanging this data during the course of mining project enables teams to understand how to improve efficiency and not repeat operations or measurements.
As innovators in the mining sector, Normet has designed intelligent software that works with spraying robots and underground equipment to achieve digitalised and sustainable underground mining and tunnelling. Scanning technology is one crucial area of data monitoring that continues to grow, with a focus on accuracy, simplifying use, and reducing overall excavation time.
Scanning technology aims to ensure safety with optimised tunnel support using sensors that monitor and control applied thickness. This data is then transferred to site office teams via wireless LAN networks. Normet’s SmartScan combines this sensor technology with Normet sprayed concrete equipment. Using 3D laser scanning technology, SmartScan automates the process and eliminates the need for probes to conduct manual calculations.
The automated calculations and monitoring of applied sprayed concrete thickness improves efficiency and reduces wastage, as well as allowing operators to remotely scan areas where repairs and concrete application may be needed. Once scanned, the data is transferred to the cloud where it can be visualised to show concrete thickness in real-time. This visual data can be exported for retrospective analysis or automatically generated concrete thickness reports.
SmartScan works in conjunction with three variations of Normet’s SmartSpray technology. SmartSpray Lite utilises a spraying nozzle that maintains its position to spray the concrete at the target surface. Operations are controlled from a single joystick to simplify use. The SmartSpray Pro has an automated nozzle so that operators only need to control the distance from the target and move between segments. The ProPlus calculates the path to automate the entire process, including distance and speed for optimal concrete layering.
Normet also offers a broad portfolio of wet concrete and dry concrete spraying equipment for mining and tunnelling applications. The wet concrete Spraymec range are electro-hydraulic self-propelled mobile concrete sprayers, including the NorRunner 140 DVC, Alpha 1430 PC, Alpha 30, LF 050 DC, MF 050 VC, SF 050 D and 8100 VC. For dry concrete applications, the company offers the Normet Piccola and Normet GM.
Looking to the future, concrete spraying will become increasingly automated and in many cases, entirely remote. Remote operations are much safer, especially in mines where deeper excavation is being carried out. Using battery-driven remote control vehicles and smart technology such as the SmartScan and SmartSpray, operators will be able to carry out their work in a way that is safer, more efficient and more sustainable than ever before.