Mines are increasingly digging deeper to access unexploited minerals, and deeper mines present a whole host of challenges, including rockbursts, large deformation, squeezing and creeping rocks. With this in mind, rock bolting and strata reinforcement is more important than ever, and it may not be easy to rely on traditional methods
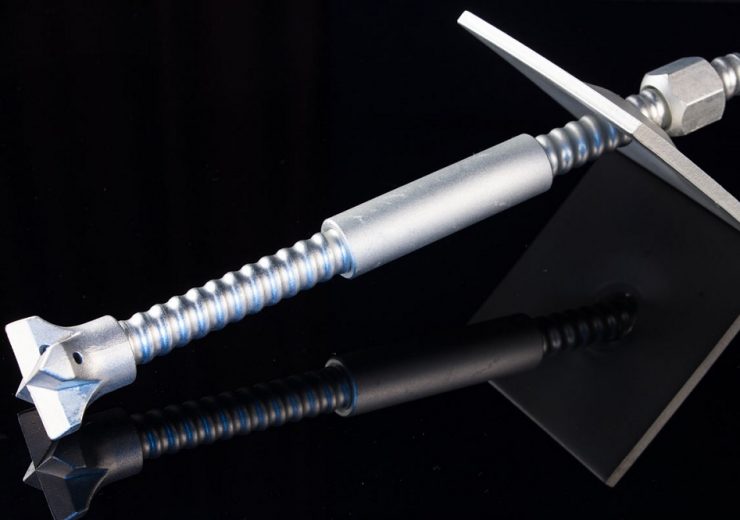
Normet Self-Drilling Anchor system (Credit: Normet)
Mines are increasingly digging deeper to access unexploited minerals, and deeper mines present a whole host of challenges, including rockbursts, large deformation, squeezing and creeping rocks. With this in mind, rock bolting and strata reinforcement is more important than ever, and it may not be easy to rely on traditional methods.
Normet is an innovative company whose dynamic D-Bolt has not been matched, despite attempts from the competition to reverse engineer a similar product. However, it is Normet’s range of self drilling dynamic bolts (SDDB) that really has the future in mind.
A challenge with using traditional bolts is that a hole must be drilled before the bolt and grout are inserted, and with rock that deep being under so much stress, there is the risk that these drilled holes will not stay open.
Additionally, fractured ground allows for water ingress, which can dilute the cement grout or polyester resin being used. Normet’s SDDBs overcome this problem as they can be drilled directly into the rock, making them ideal for fractured ground or unstable strata.
According to Martin Petranek, director of products and production for rock reinforcement at Normet: “Using a self drilling bolt does half of the installation for you, and then all you need to do is use a pumpable thixotropic grout or resin to bond the bolt. At Normet, we offer hydrophobic sodium silica-based resins, so it won’t be diluted or flushed by water ingress, and is also able to flow through cracks to consolidate the rock.”
The deformable resin is able to absorb some of the energy from the rock, further reducing the risk of bursts. As for the bolts themselves, the installation of these self drilling bolts can be fully mechanised, so workers can stay back at a safer distance.
“You can use bolting machines that are able to install these bolts, and the operator is protected in ROPS/FOPS certified cab. Major mining manufacturers are already looking at developing new equipment for installing self drilling bolts, so it’s really what the future demands,” Petranek says.
With other competitors entering self drilling bolts into the market, what is it about Normet’s portfolio that sets it apart? Petranek explains: “Where Normet is ahead, is that we offer variety with these bolts. We have two basic designs based on the material property, and we have several models made of these two basic models that differ in shape.
“We have the bolt made of seamless tube and a thread on the outer side that is rolled evenly on the left and the right of the tube. These bolts are commonly either 1.5m, 2m, 2.4m or 2.5m, and they can be extended with a coupling. By offering an extendable solution, we are able to substitute cable bolts if you need to drill much deeper into the rock.
“We are not limited to any size, it’s very customisable. Bolts can be tailored to customer demand, for length, diameter, even the length of the threaded section. We can also customise what kind of drill bit they want to use, as bolts will need to be able to drill a hole that is bigger than a coupling if the customer is doing extended drilling, but still kept as small as possible to limit how much grout that you need.”
It is not just the customisable design that sets Normet’s locally ancored self drilling hollow rock bolts apart from the competition. Normet has paid close attention to using materials that are best suited for mining applications.
“Conventional rock bolts are usually manufactured from ordinarily construction steels, which is not really ideal. It has certain load-bearing parameters, and is fine for applications such as concrete reinforcement where it is pretensioned, but for mining there are challenges with the impurities in the steel.
The steel is rolled in just one direction when it is manufactured into a bar, and the resulting impurities can make it very weak because of the microscopic bubbles in the steel. The material that we use for dynamic bolts is homogenised, which requires a different treatment to get a uniform structure and is much stronger.”
Visit Normet’s website for more information about the D-Bolt and Self-Drilling Anchor systems.