Final packaging of nuclear waste materials requires final welding to seal transport containers. Ensuring this process is safe, secure and of a consistently high quality prompted the development of a new automated mechanised approach, writes Richard Howells, Innovation Development Director, Jacobs
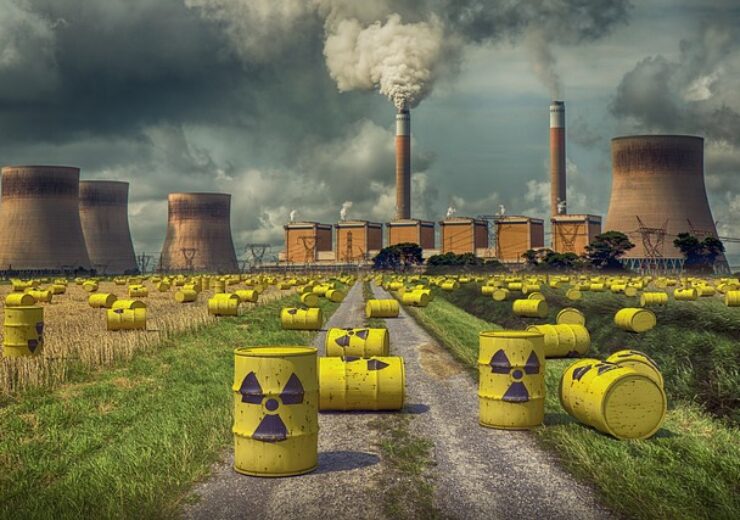
Analysing how TANICS is transforming nuclear waste container welding with automation. (Credit: Enrique from Pixabay)
To avoid the need for repackaging at the storage location, highly radioactive material must be transported in sealed stainless steel 316L containers, which are usually welded to provide a robust and predictable lifetime seal.
For site-to-site transportation, containers are generally housed inside an outer package or flask which is licensed for transport. However, in some cases, these containers are required to be capable of providing an additional layer of containment due to the nature of the material being transported. The same containers are also used for handling on-site and are required to resist impacts in case of collisions during transfer. It is therefore important that they can maintain structural integrity, criticality-safe geometry and, ultimately, containment during both normal operations as well as in accident conditions. These containers require a welded closure with sufficient structural capacity to maintain containment even if it is damaged.
Producing welds of the required quality during the initial container fabrication process is relatively straightforward when carried out by sub-contractors with the appropriate levels of quality required. However, the final closure weld – fixing the lid to the container body – must be performed remotely using a mechanised process. This is easier said than done – the problem is how containers packed with nuclear material can be sealed remotely in a reliable and cost-effective manner that meets the requirements of both transport and long-term storage. It requires significant expertise which is not often readily available.
Furthermore, the current range of equipment available for remote or mechanised stainless-steel welding is generally aimed at fixed-diameter welding using large bespoke static equipment that can only be deployed on-site if the facility is a new build specifically designed to accommodate it. This limits the application of welding on nuclear sites within existing facilities, and it is also a challenge where there is the need to weld different container diameters and a variety of weld types.
To address this challenge, Jacobs, the international engineering services company, together with welding specialists Langfields Ltd, part of the Envoy Group, developed TANICS – The Automated Nuclear Irradiated Container Solution – an automated, robotic welding solution for the nuclear industry.
Developing TANICS
Jacobs and Langfields, who have worked together on nuclear container welding for many years, made a joint decision to develop a site-deployable solution which had the flexibility to weld containers with a variety of diameters and weld configurations. Designed with safety and quality assurance as paramount considerations, TANICS is a complete package capable of delivering a high-integrity butt weld and associated qualifications for scalable containers.
Automated industrial robots are commonplace, especially in the automotive industry, but they are not suitable for nuclear applications because they mostly perform stitch welds, not the closure welds required on stainless steel radioactive material containers.
The welding of the containers will take place inside shielded cells to protect the operators. These cells are built ad-hoc to provide operations staff with shielding from fuel material with a potential dose uptake of up to 30 Sieverts per hour. Although the welding control system contains a substantial number of electronic components which are sensitive to radiation, the welding robot will be located within the cell. It must therefore be protected from excessive radiation dose. This will be achieved in three ways:
- The majority of the equipment, such as control panels, will be located outside the cells with the operations staff
- The robots will be located behind shielding until the time they are required to weld
- The container will be shielded as much as possible during welding operations (leaving the welded areas unshielded) to further protect the robots
The design of these features has been analysed and verified by Jacobs shielding experts using specialist software and
is also underpinned by radiation exposure experiments in Jacobs’ laboratories.
The weld inspection robot is fitted with cameras and an eddy current inspection system so operators can see footage of the entire weld from different angles to assess the weld profile. Quality control is also underpinned by data management, with all data and communications protected by a high-grade cyber security system.
Welding flexibility
TANICS can perform full penetration butt welds with a unique system that can displace oxygen within a cylinder fitted with a single method of entry/exit. This mitigates the risk of root weld oxidation which occurs when using conventional purge techniques on a nuclear container. As a result of this, the risk of failure and expensive re-work is mitigated.
The system also allows inspectors to sign off weld inspections without the need to attend the site in person. This reduces the costs of travel to the site and accommodation and allows verification to take place efficiently without having to wait for individuals to arrive in person.
TANICS can weld a variety of container diameters and can perform full and partial penetration butt welds in addition to fillet welds in both vertical and horizontal orientations. Existing mechanised welding systems (such as Orbital heads) are fixed diameter machines capable of a single weld geometry such as butt welds. If a fillet weld or different diameter is required, then more machines must be purchased increasing costs.
The system incorporates several features to assist with maintenance when the robot is installed, including a grinding assembly located within the cell to maintain the profile of the tungsten electrode; and a capacity of up to 30 metres of welding wire to complete the required number of containers. Currently, there are no other systems capable of being deployed on client sites to do this work in a highly radioactive environment.
Qualification and use
TANICS is qualified in accordance with the European harmonised codes (BS EN ISO 15614-1) and has been dual coded with the American Society of Mechanical Engineers (ASME) IX, by an independent UK third-party body. The qualification process used the acceptance criteria PD5500 Cat 1 and Sellafield Build Level 1. As a result, TANICS is a Technology Readiness Level (TRL) 8 technology.
“The welds produced using TANICS were independently qualified in the UK and Germany and have now been endorsed by specialists from Sellafield Ltd. This shows that the system has the potential to set a new benchmark for automated welding in the nuclear industry,” said Langfields Projects Director Wayne Griffiths.
The system has been endorsed by the welding subject matter expert at Sellafield Ltd and is capable of being deployed to any site to seal nuclear containers reliably to a high acceptance criterion, in doing so this system is capable of sealing containers to meet both transport and 100-year storage requirements.
As the nuclear industry increasingly needs to move and store nuclear fuel material using bespoke containers, TANICS offers a number of benefits over existing solutions, including its repeatability, flexibility and efficiency, and it is suitable for transport and long-term storage.
Equally importantly, it is a safe, effective and efficient means of achieving the required quality of the weld and avoids putting operators in harm’s way. This innovation, developed to meet the requirements of the UK’s nuclear decommissioning mission, has the potential for export to other nuclear markets, supporting the exports and jobs ambitions of the UK’s Nuclear Sector Deal.
David Campbell, Technical Manager for Sellafield Ltd, concluded: “This is an exciting development where a high integrity welding process can be deployed remotely and adapted to suit a variety of container sealing activities and could almost be classed as off-the-shelf.”
This article first appeared in Nuclear Engineering International magazine.